Raku Pottery Tips & Tricks
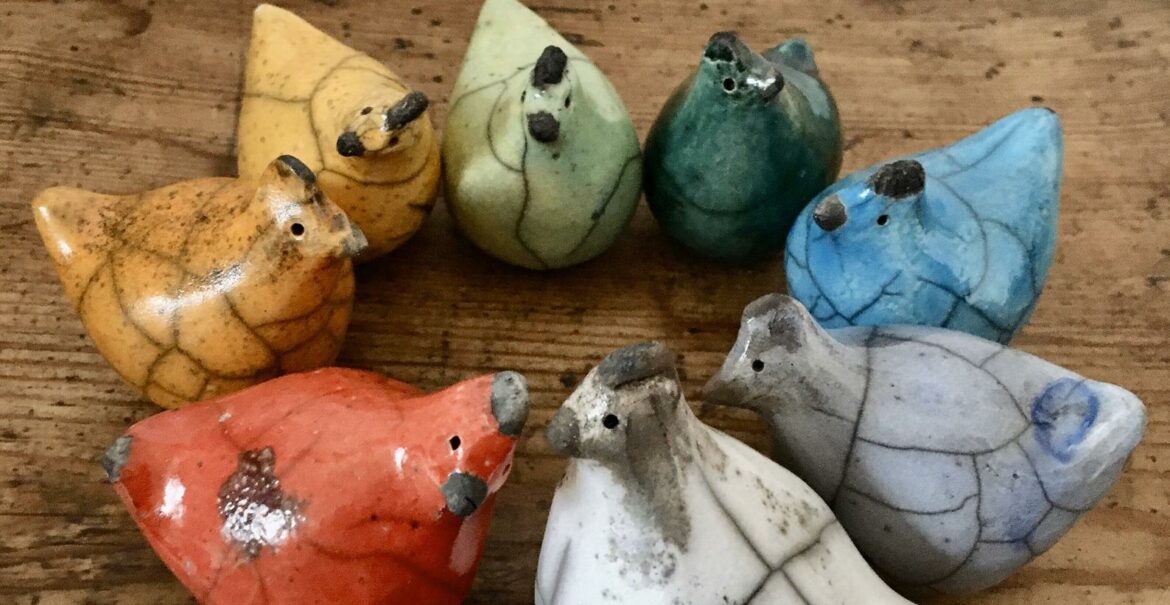
Raku is a popular type of Japanese pottery that was used in tea ceremonies in Japan. Many tea masters liked Raku because the objects such as chawan tea bowls were simple and pure.
With a rich history that dates back to 1580, this Japanese ceramic form remains to be a fancy art for many. Here’s everything you need to know about raku pottery:
Table of Contents
What is Raku Pottery?
Raku is a low-firing process that was taken from the traditional raku firing in Japan. Western-style raku firing often includes taking out pottery from the kiln with the bright red heat and putting it in containers that have flammable materials.
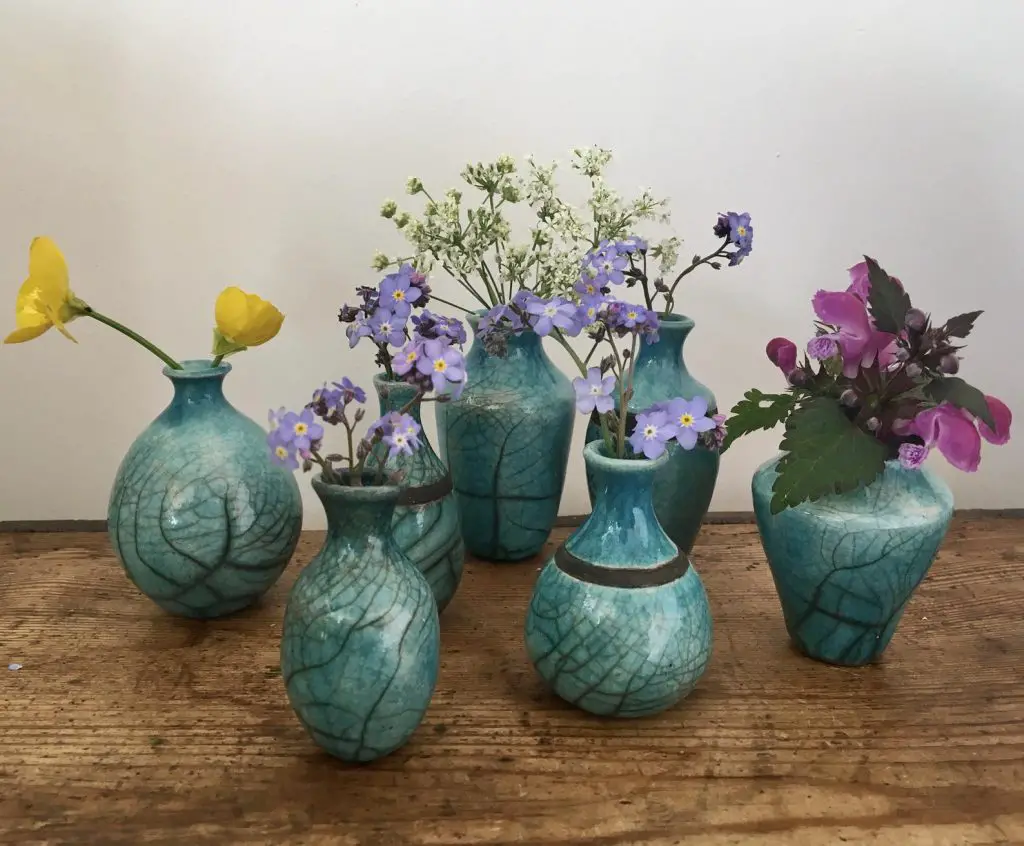
After these materials burn, the containers are shut. As a result, the colors in the clay bodies and glazes are affected due to the intense environment. This extreme thermal shock also results in cracks. The original Japanese raku style was inspired by the life and tea ceremonies of Buddhists.
History of Raku Pottery
Sasaki Chōjirō was the one who started Raku pottery. He was encouraged by Sen no Rikyū who was a tea master and his close friend. Chōjirō made bowls that were similar to the colorful Chinese ceramics during that period. However, Chōjirō’s bowls were mostly black or black without any sense of movement or design.
In the past, drinking tea was considered as a celebration by noble people. They drank with grandeur and held lively tea tasting contests often. Later on, Zen Buddhism started in Japan, which brought about chanoyu or sadō – a more observed and solemn ceremony.
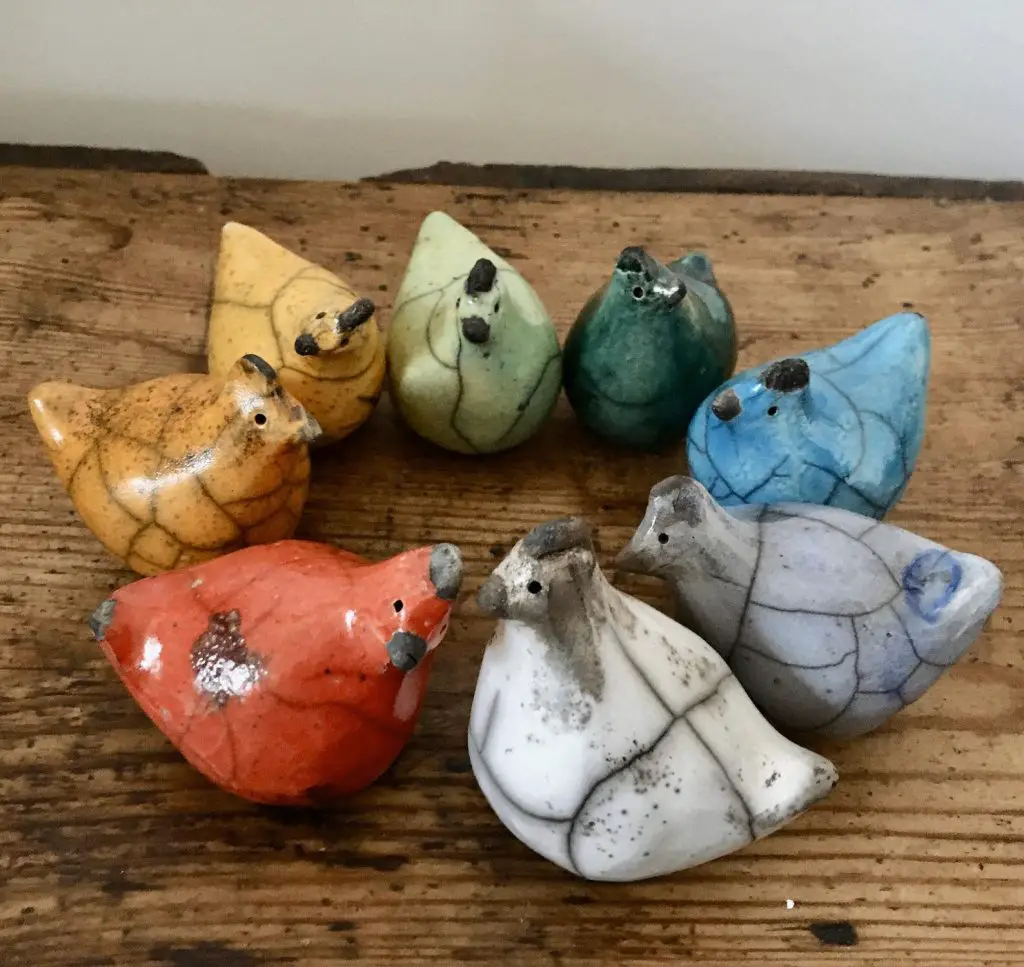
Rikyū combined the Zen and Taoism principles to chanoyu. This resulted in the creation of Wabi-cha, which was a tea ceremony that focused on appreciation and simplicity. Chōjirō made bowls that represented Rikyu’s philosophy on tea. The Raku dynasty started when his bowls were recognized by warlord Toyotomi Hideyoshi.
Types of Clay for Raku Pottery
Any type of clay can be used when raku firing. Here are some of them:
Grogged Clay
Grogged clay is often suggested for raku pottery because it can withstand the temperature changes during raku firing. Grog is a kind of clay that is heated and turned into granules and powder. Then, it is combined into clay that is not fired. This results in more durable clay.
Also, when the clay dries or is fired, grog lessens the shrinking of the clay. It also makes the clay more resistant to thermal shock and temperature changes because it becomes firmer. This is the reason why many opt for this type of clay for raku firing. Nevertheless, when a potter’s wheel is used, it can be too rough on the hands.
Stoneware Clay
Many potters use light-colored stoneware clay. When doing raku pottery, this type of clay makes a great contrast on the carbonized parts.
Moreover, this clay will display your desired color for your raku beautifully when you utilize alcohol reduction raku.
T-Material
T-Material is white grogged stoneware clay that is a popular option for potters. It is great for raku pottery because it has low shrinkage and thermal expansion and is light in color.
The Raku Firing Process
The raku firing process is faster compared to normal firing because it only takes 1 to 2 hours. Normal firing can last for 24 hours.
The first step in the raku firing process is glazing the ware with a special raku glaze. You can buy this from pottery equipment suppliers or some craft stores. This glaze is designed to have a low melting point, so it can take around an hour to melt. A thin layer of the glaze is recommended for raku pottery to achieve a faster melting point and effect.
Next, it is time to load your wares to the kiln and raise the temperature to 1,850 degrees Fahrenheit which needs to last for 1 hour. You can check on them every 15 minutes and after 45 minutes when firing was started to make sure that the process is done correctly. If you see the glaze bubbling, it means you are doing the firing process right. After seeing that the glaze is bubbling, you can leave it for 15 minutes more.
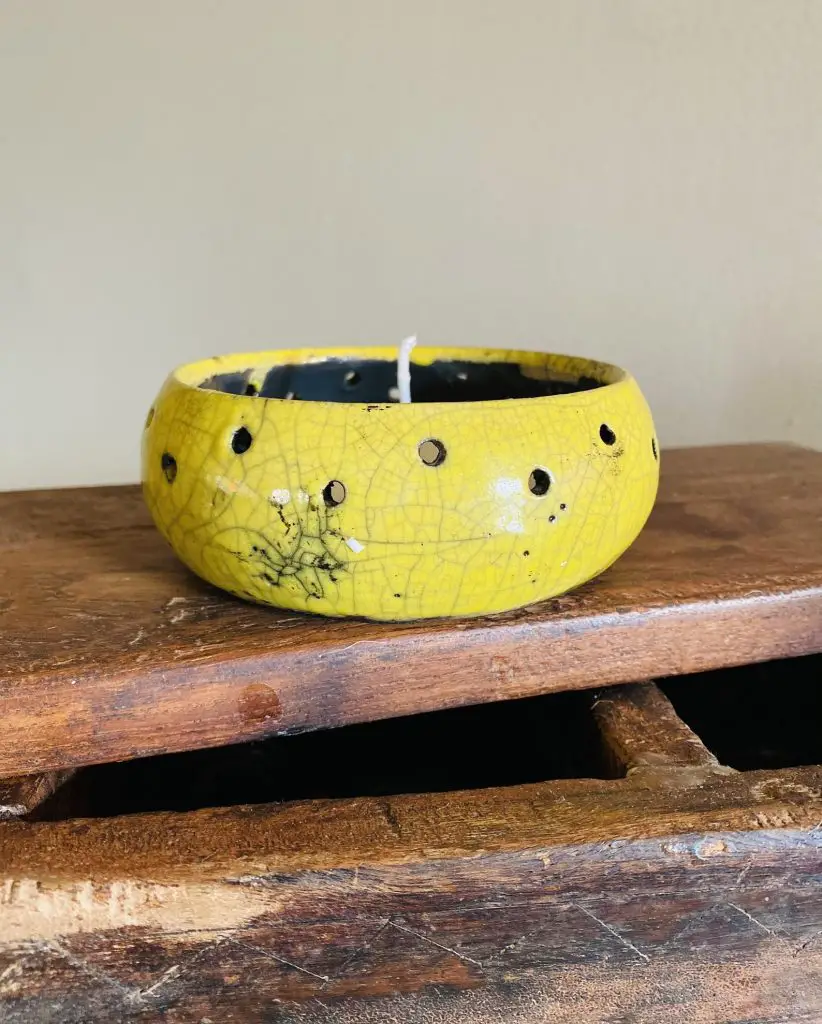
You will now take your ware from the kiln when the surface is liquid, red, and shiny. While you wait for the kiln to complete the process, you can prepare the container that you will use to decrease the oxygen to your ware.
You need to add sawdust or shredded newspaper to your metal container. You have to use a metal container that is slightly larger than the ware you are placing inside. You can get a good color spectrum when the area surrounding the ware is tighter since the oxygen is reduced.
After your wares get a red hot glow, three people are needed to do the raku firing. The first person will open the kiln door, the other one will pull your wares out using tongs and transfer them to the metal container, and the third person will be the one to shut the lid of the metal container. You have to keep in mind that using protective wear such as heat-proof gloves is very important since you will be handling very hot materials.
When taking out your wares from the kiln, the door should be shut after every piece is taken out to maintain the heat needed. It is recommended to move as fast as possible when transferring the pieces to the metal container. The third person should be the one to fire the sawdust or shredded newspaper and put the lid fast so that the wares can be smoked.
You just need to wait for several minutes for the smoke to leave an impression on your wares. You have to be extra careful when taking the lid off since the smoke will be very high and can cause burns if not done properly.
Removing the wares must be done with great caution. You can pour hot water to cool your wares and take them out using tongs. Then, you drench them using a bucket of water. After that, you must see the effect of raku firing on your wares.
Extra Tips on Doing the Raku Firing Process
- You can glaze your wares the day before you do the raku firing process so that you can focus more on the kiln and not rush on glazing.
- Give enough space around your wares. This will make it easier to handle the pots with tongs and safely take them out from the kiln.
- Leave a clean space at the base of your wares for the drips from the glaze.
- For flat pieces such as tiles, you can raise them using poles so that it is easier to handle them using your tongs.
- While waiting for the kiln, you can position your wares around to warm them up.
- You can wait for a little bit before removing your wares from the kiln if you want a beautiful crackle.
Is Raku Waterproof?
Raku wares are not waterproof. That is because the raku firing process is completed very fast using a low temperature. Moreover, raku wares are coated using many materials. When raku wares are exposed to water, they will eventually disintegrate due to seepage.
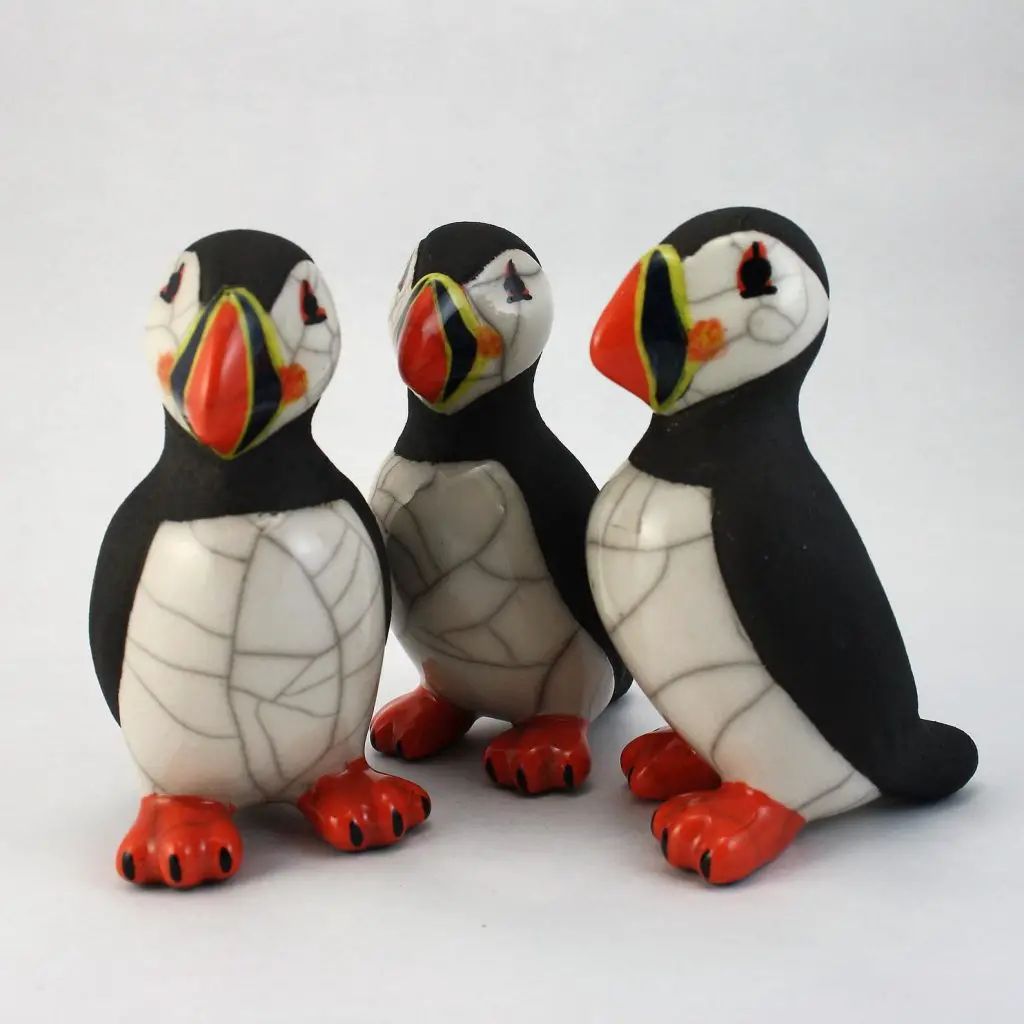
Nevertheless, there are methods to make raku wares water-resistant. You just need to remember that raku pots cannot be waterproof even when they are glazed.
Is Raku Dishwasher-Safe?
You should never wash your raku wares using your dishwasher. It is best to wash them using your hand using regular dishwashing liquid and a soft and gentle sponge. Also, you should not use abrasive paste or brushes.
Another way to clean them is by immersing the wares in warm water with vinegar to protect them from bacteria.
Raku Pottery and Vitrification
Once the kiln has reached 1,730 degrees Fahrenheit, the clay becomes sediments. Vitrification is the process where wares become hard. This process happens when the clay reaches a temperature enough for its glass-forming elements to melt.
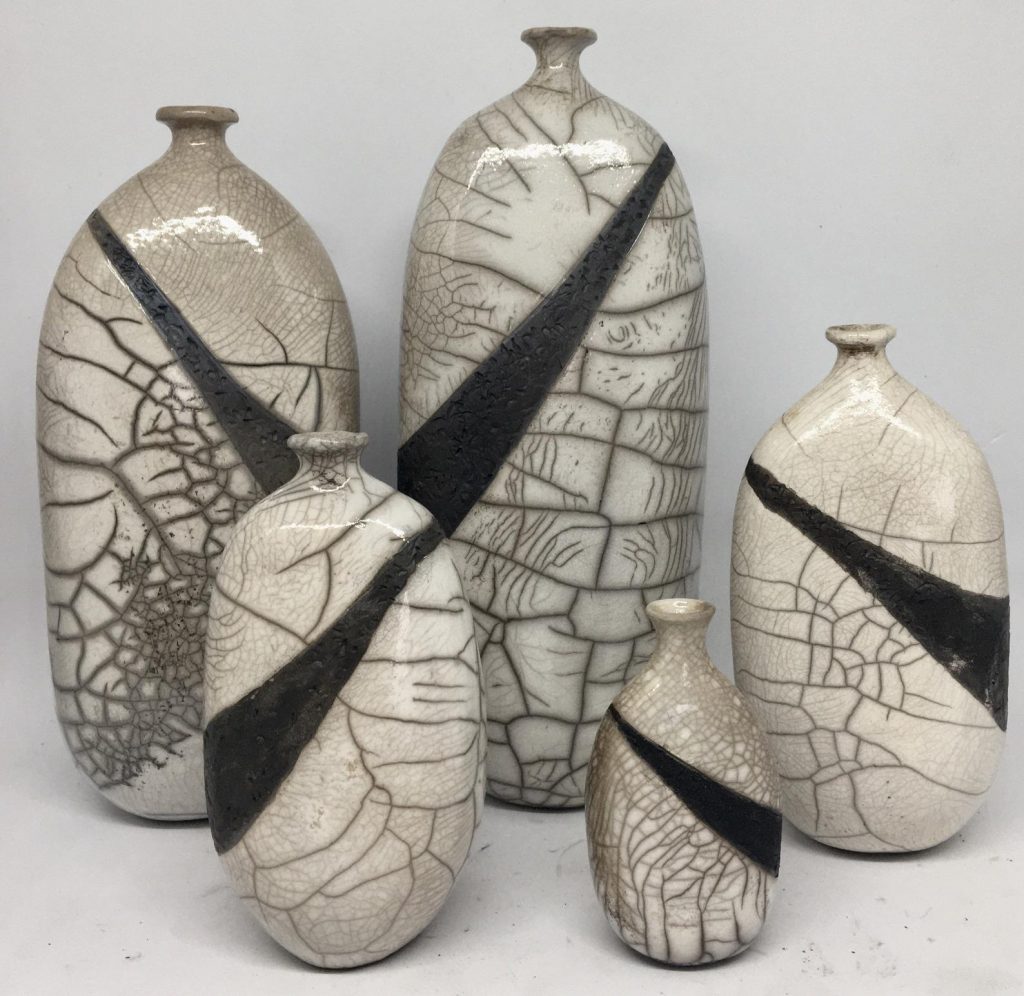
In vitrification, liquid moves into the clay particles and the spaces where the particles close. When the temperature cools down as the firing is about to finish, the liquid becomes solid in the areas enclosed by the particles resulting in the clay becoming waterproof and dense.
During the raku firing process, vitrification occurs at temperatures greater than what is achieved. Because of this, raku pots are absorbent, making them not waterproof.
Conclusion
Finally, you understand what raku pottery is and how it came about. This form of pottery is famous because of the impressive process of firing it. However, it can be nerve-wracking because of the need to take out the wares from the kiln while it has a red glow.
For many, this pottery is considered to be a gem because of its unique and impressive pottery process. No wonder many potters are amazed at raku pottery.