5 Main Types of Clay for Pottery (Explained for Beginners)
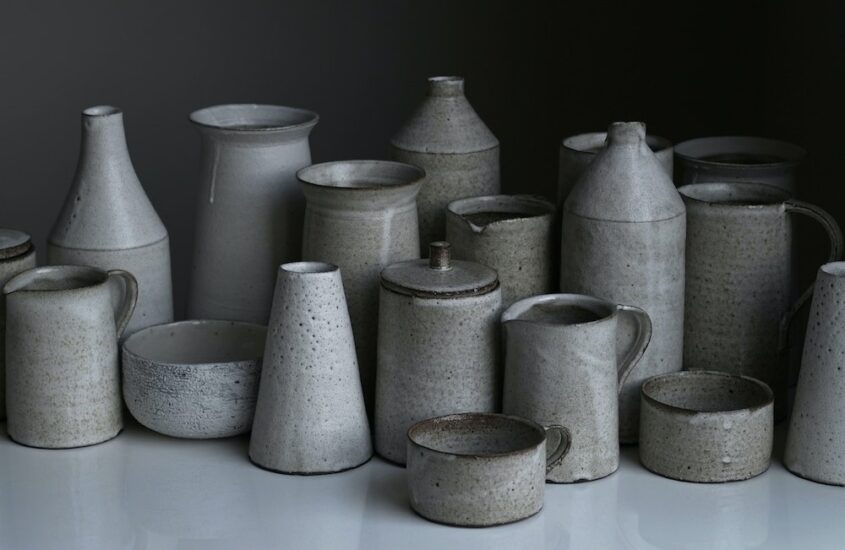
For whatever type of pottery a person has taken an interest in, the first most important component needed is the clay.
Furthermore, knowing the specific type of pottery you’re interested in will help you narrow down your options for clay.
To someone new to pottery, the thought that there’s more than one type of clay may be discouraging. However, constant pottery projects will teach us that some clays are just better suited for some types of pottery than others.
For some pottery projects, the requirements may vary in respect to melting temperature, its components, appearance, etc. As a result, it is good to have a good grasp of the different types of clays that are out there.
Below are the main types of clay for pottery.
Table of Contents
Oil-based Clay
Oil-based clay is arguably the favorite of artisans who specialize in any of the expressive forms of art. This type of clay comprises various kinds of oils mixed into the clay till it is homogeneous. It is easy to manipulate, highly plastic, and can be reused.
Animation artists especially love oil-based clay because it is malleable and non-toxic.
There’s a catch, though. Due to the interaction between temperature and oil molecules, the molecular structure of oil-based clay can be affected by temperature.
When exposed to high temperatures, oil-based clays melt and become runny, and when cooled, they harden. It has often been described as waxy, except that it is also grouped with other such clays known as non-hardening clay.
It is not recommended for use in making ceramics, for obvious reasons.
Water-based Clay
Also referred to as Walter E. Disney clay (WED) clay, this type of clay is as malleable as oil-based clay. In the case of WED clay, the oil in oil-based clay is substituted for water. This type of clay is ideal for quick sculptures, wax-like figures, live models, etc.
WED clay also falls under the category of non-hardening clay, and it requires enough moisture to remain soft and pliable.
When exposed to high temperatures, WED clay may explode in the kiln due to its high moisture content. There’s no point in sun-drying it first, its composition does not allow for firing.
When exposed to low temperatures, the water molecules may freeze, allowing them to become firm. However, when it melts, the structure changes and creates fissures in the pottery.
When the water dries off, it may become flaky and may break, so keep it hydrated.
Polymer Clay
This type of clay falls under the category of hardening clay. It is more accommodating of high temperatures than oil-based and water-based clays.
It is commonly used as decorative pieces, accessories for some sculptures, art projects, for making models of live objects, etc.
Although the polyvinyl chloride polymer content allows it to harden when fired, it also means that it loses its malleability. The alternative to this clause, however, is that the clay works best when fired at low temperatures (between 130°C – 135 °C). This temperature range is achievable with a kitchen oven, and it prevents the clay from shrinking.
Although it is considered unsafe for consumption by some, it goes without saying that it should be kept away from babies.
Dough Clay
Also known as “Playdough”, this crowd favorite is very malleable, non-hardening, non-toxic, and can be whipped up at home. It can be used and reused, and it is completely safe for children to play with. Some companies even make edible and inedible versions of the clay.
This type of dough is the favorite of children and elementary school teachers. It has also been recommended by psychiatrists for relieving stress and working through stressful situations.
Dough clay can be made at home by combining flour, oil, water, cornstarch, and some salt. For a variety of colors, you could add food coloring and flavoring (for the edible ones).
It is not recommended for use in long-lasting objects, as it can crack and flake, so enjoy reusing them as you see fit. Also, depending on what you intend to make, the dough can be baked or heated under low heat (less than 100°C). This helps it retain the firm, solid form that you desire.
Ceramic Clays
These are the different types of clays that are used in making pottery or ceramics. There are many different types of ceramic clays out there, and finding the most suitable one can be a hassle. However, you’ll soon learn that although there’s a lot of them, they are also distinguishable.
One neat thing about most ceramic clays is that they are ideal for use in very high temperatures. For example, porcelain clay has a firing temperature of 1000°C, and fire clay has a firing temperature of above 1600°C.
These ceramic clays include:
1. Earthenware Clays
What Earthenware Clays Are?
Earthenware clays are the most abundant and commonest type of clays. They are said to be among the oldest type of clay to have been used in pottery. This type of clay has the characteristic of being very sticky, and as such, it is extremely easy to work with.
Earthenware clay is also known as terra cotta clay, and it mostly naturally occurs as a red clay body. Terra cotta is very popular as an ingredient for making planters, some traditional sculptures, and figurines.
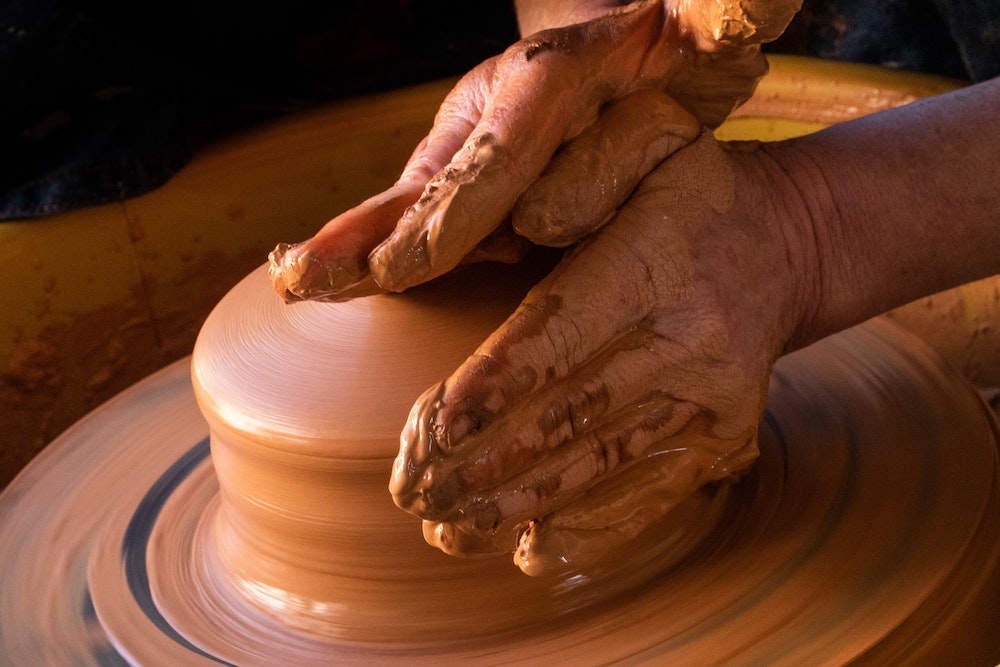
Earthenware clay can also be white, yellow, brownish-yellow, or tan.
Typically, earthenware clay produces porous wares when fired, which makes it ideal for use as planters.
What Earthenware Clay Is Used For?
Knowing that earthenware clay produces porous wares, it is often used to make plant pots, terra cotta, figurines, and so on.
Furthermore, earthenware clay can be glazed and baked so that it can hold moisture. This type of earthenware, although less porous, is used to make bowls, pots, serving dishes, etc.
How Earthenware Clay Is Used?
Typically, earthenware has low silica content, so it does not easily lead to the formation of glass or become vitrified. At a temperature of about 950°C and 1,100°C (or 1,745°F and 2,012°F), earthenware clay matures.
This high firing temperature occurs as a result of the presence of mineral impurities in the clay.
Earthenware clay has a high level of plasticity, so it won’t slump or collapse when being worked into pottery.
To use earthenware clay, you need to:
- Prepare the clay (knead it and moisturize it alone, or add some silica to make it more vitreous)
- Throw on a pottery wheel and fashion or make pottery
- Sun-dry the pottery for 2 – 3 days
- Bake in a kiln. At this point, the bisque is porous and can be used without glazing.
The last two points are optional and are for making potteries that are used to hold or retain water and other liquids
5. Glaze the pottery and air-dry it
6. Fire the bisque again (at about 950°C)
What Earthenware Clay Is Made Of?
Earthenware clay has a composition of iron, and a few other mineral impurities, which work to give it its unique properties. This perfect blend of mineral impurities and iron go a long way to alter the physical properties of the clay.
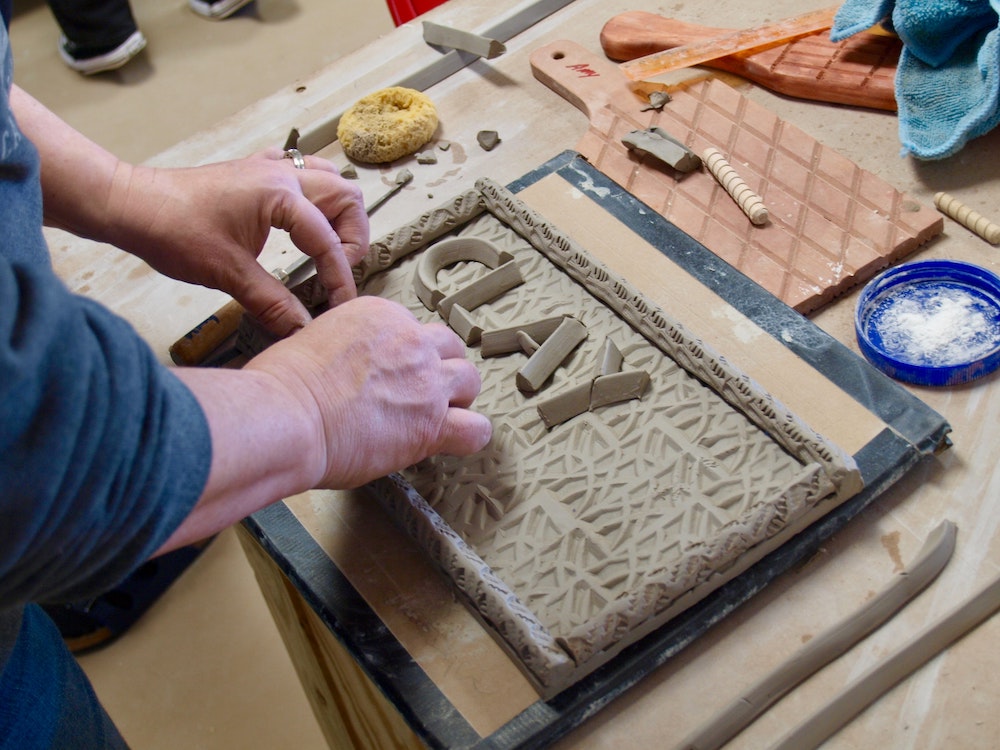
Also, these extra components play a role in the maturation temperature of the clay when it is fired.
2. Stoneware Clays
What Stoneware Clays Are?
Stoneware clays are a special type of clay that appear white or grey when water is added to them. They are plastic or malleable clays, so working with them is easy.
Typically, the melting point of stoneware clay is much higher than that of earthenware clay (between 1000°C and 1380°C).
Stoneware pottery is an umbrella term for potteries that have been fired at temperatures between 1000°C and 1380°C. What happens is that the molecular structures of these potteries change to become like that of stone. When their structure changes, so do their durability and their lifespan.
Stoneware pottery is the least type of pottery to be affected by factors like age, breakage, wear, and tear, etc.
What Stoneware Clay Is Used For?
Generally, stoneware clay has more glass-forming particles than earthenware, so it has almost zero porosity, is more durable, and lasts longer.
Stoneware clay is used to make vases, stone tables, some bricks, and so on.
How To Use Stoneware Clay?
The plasticity of stoneware clay gives it a wide range of things it can be fashioned into successfully. However, the process of using stoneware clay is similar to the process of using earthenware clay.
- Prepare the clay (knead and moisturize it)
- Throw on a pottery wheel and fashion pottery
- Sun-dry the pottery
Stoneware clay does not require too much water, or it may become runny. A little moisture from time to time will suffice.
What Stoneware Clay Is Made Up Of
As stoneware does not result from the direct erosion of specific parent rock, it often contains impurities. Some of these impurities are silica, feldspar, ball clay, and quartz.
In man-made forms, stoneware is also mixed with ball clay, as well as fire clay to increase its melting point.
3. Ball Clays
Ball clays are the type of clays that work so much better and in reality, are more useful, when they are mixed or used with other types of clays. When used as a standalone, ball clays are unable to go through the drying and firing process without shrinking considerably.
When mixed with other types of clay, however, they help to influence the workability of said clay. This means that they make whichever clay they are added to, more plastic, and as such, more flexible to work with.
Ball clay comes in a powdery white state and has a few caveats. One of such caveats is that it dries up quickly, and shrinks a whole lot. Indeed, all clay dries, but ball clay dries the fastest. This means that ball clay potteries are more prone to explosions in the kiln.
What’s more, potteries with ball clay are prone to cracking if the moisture is not removed at the same time.
What Ball Clay Is Used For?
Ball clay is perfect for porcelain wares when mixed with porcelain clay. For example, it can be used to make flooring tiles, toilet bowls and tanks, and some tableware
It can also be used to make decorative accessories for porcelain pieces. Take note, however, that when the firing process is incomplete, the color of ball clay changes to a brownish-yellow or tan. When the firing process is allowed to go on without any interruptions, the resulting color is a fine white.
Also, ball clay can be mixed into a paste and used as a decorative glaze for some terra cotta.
How To Use Ball Clay?
As we have already established that ball clay works best when mixed with other types of clay, using it in its mixed state is easy.
- Mix the ball clay (dry or wet) into the clay base
- Knead till you get a homogeneous mass
- Throw on a pottery wheel, or fashion by hand. Voila!
What Ball Clay Is Made Up Of?
Ball clay is usually mined from the soil or the parent rock. As a result, the majority of non-clay components of ball clay would be organic matter like dirt.
Also, ball clay contains little amounts of alkaline earth metals like magnesium and calcium and a moderate amount of lignite (brown coal with almost no carbon content).
4. Fire Clays
This type of clay is unique in its composition, appearance, as well as in its melting point. Fire clay is aptly named after its extremely high curing temperature (beginning at 1600°C). In terms of appearance, fire clay is brownish yellow or grey, and it lightens when fired. It is usually sold in its powdered form and has coarse particles.
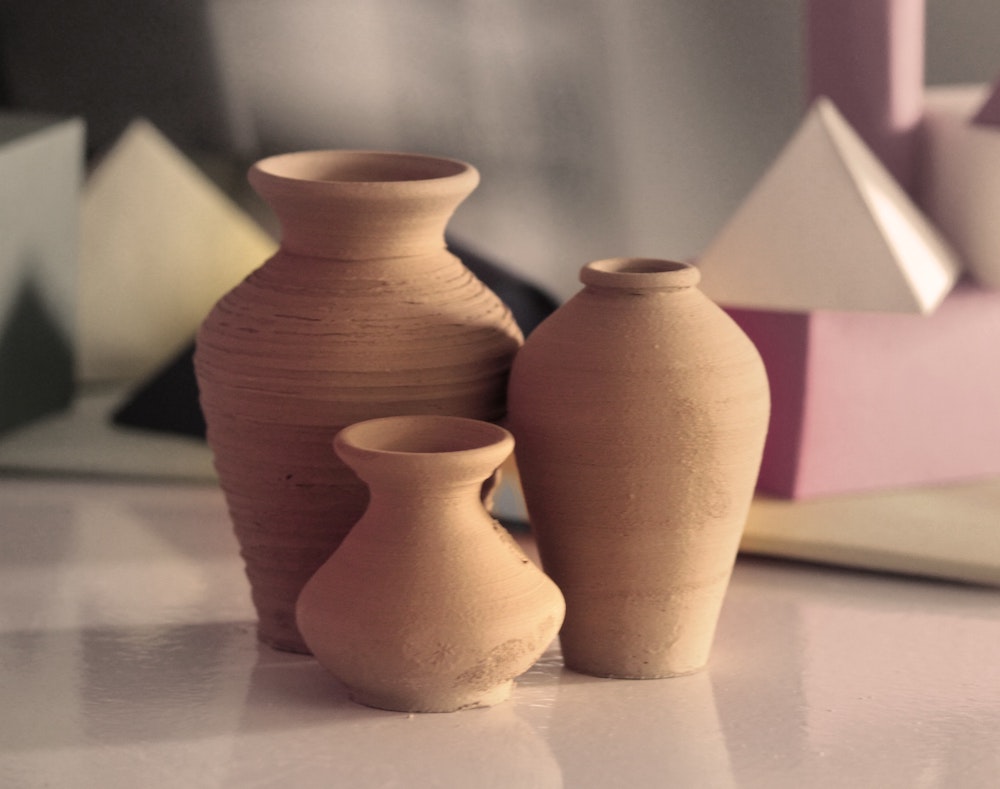
Fire clay is often described as a refractory type of clay because it can endure high temperatures without getting destroyed.
On its own, fire clay is not ideal for use as a standalone base for pottery, probably due to its high firing temperature. One factor that may contribute to its high melting point is that it sometimes contains trace amounts of iron. If fire clay has iron traces in it, the end product appears speckled after it has been fired.
In addition to their high melting point, fire clays are one of the purest types of clay.
What Fire Clay Is Used For?
As a result of its high melting/ firing point, fire clay is ideal for items and apparatuses that work with high temperatures. For example, fire clay can be used to make bricks for chimneys and fireplaces, kiln structures, etc.
When fire clay is in its paste form, it can be used to fill up holes in walls, kiln bricks, etc.
How To Use Fire Clay?
Fire clay is best used when combined with another clay body, the most ideal being stoneware clay. To use fire clay,
- Get a base clay body
- Mix the powdered fire clay into the moistened clay body
- Mix the clay until you get a homogeneous mass
- Pour into a mold
- Bake in a kiln.
What Fire Clay Is Made Up Of?
Fire clays are notorious for their high melting temperature because it has an aluminum oxide content of over 30%. Besides fire clay also contains silica in large amounts (up to 65%).
Also, fire clay contains iron in trace amounts, usually less than 5%. The iron gives it a speckled appearance after firing.
5. Porcelain (Kaolin) clays
Porcelain clays are the type of clays used in making porcelain pieces. Although it typically occurs as a white mass of clay body, kaolin clay has been known to have various light colors like grey.
The white or almost white color it possesses makes it perfect for this purpose. What’s more, the mineral components of kaolin are in a perfectly arranged structure that allows them to withstand extremely high temperatures.
When wet, this type of clay appears greyish, and when it is fired, it takes on an even brighter color, ranging from lighter shades of grey to an off-white color, and then to white.
Due to the very fine component particles of kaolin clay, when it is stretched, the porcelain produced becomes so white, it’s almost translucent. In essence, the structure of its particles allows it to be sculpted into thin-walled pieces.
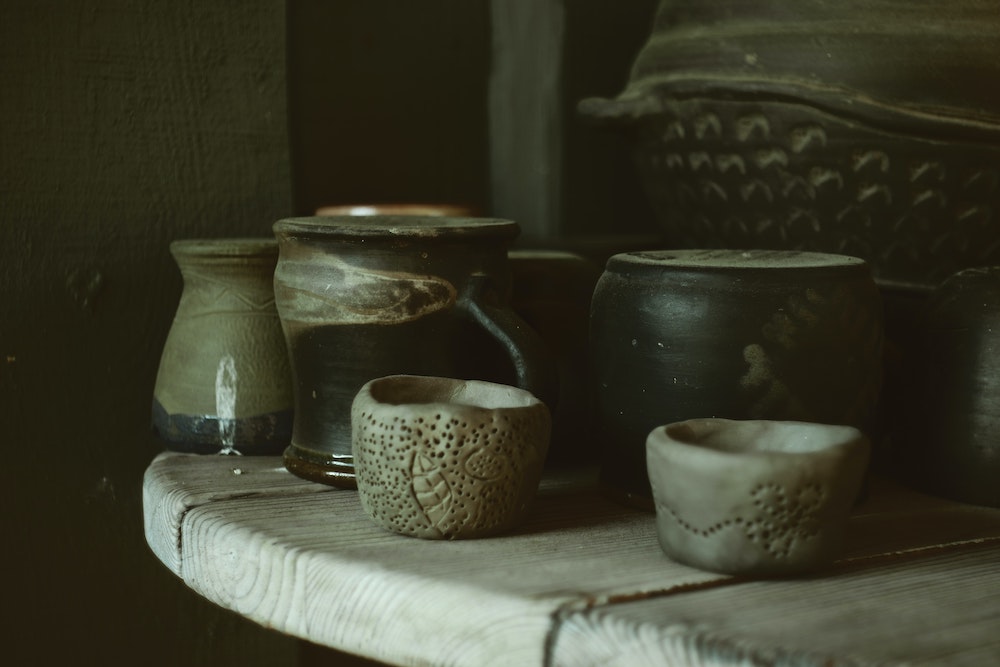
One caveat, however, is that porcelain pottery requires constant moistening because it dries out very quickly. To combat this, be sure to keep a bucket of water within reach. Too much water makes it runny and almost impossible to fashion, so go easy on the water.
Another caveat is that porcelain clay has almost no plasticity (it is difficult for it to retain the form of what it is being made into). To reverse this, sculptors often combine it with ball clay to amp up the plasticity.
What Porcelain Clay Is Used For?
The molecular structure of kaolin clay is such that it can withstand over 1000°C. Their structure and appearance make them perfect for sculptures and for making porcelain pieces. When fired, porcelain clay becomes vitrified (rid of its porosity), making it ideal for making domestic potteries. For example, it is used to make vases, china pieces, some medical apparatuses, dinnerware and cutlery, and some decorative pieces.
How To Use Porcelain Clay?
Its primary ingredient, kaolin clay is gotten directly from its parent rock, making it a primary type of clay. When fashioning it into pottery, it is advised that you combine it with a more flexible type of clay.
- Combine wet porcelain clay with ball clay
- Knead in enough ball clay to give it the required plasticity
- Moisten the clay
- Throw on a pottery wheel and create pottery.
What Porcelain Clay Is Made Up Of?
Since kaolin clay is a primary type of clay, it has an impurity content of almost zero.
The primary ingredient of porcelain clay is kaolin clay.
It also contains small amounts of quartz and feldspar, especially when porcelain clay is being artificially manufactured.
Paper Clays
This type of clay is a minor type of clay because it is unpopular and not commonly used. It is an amalgamation of clay and organic material like pulp.
This type of clay includes any type of clay that has been fused with cellulose fiber. When processed cellulose is added to bone china clay, earthenware, stoneware, etc clay, the result is known as paper clay.
In essence, paper, the most common type of processed cellulose fiber, is added to the clay. This addition fuses the paper with the clay, making it less prone to shrinkage when dried, which also means it’s not for firing.
Paper clay is used to make quick sculptures that dry up when exposed to air and a bit of sunlight. Also referred to as fiber clay, this type of clay is famous for its tensile strength and flexibility. This makes it ideal for joining other types of clay, whether they’re wet or dry.
Conclusion
In conclusion, having considered the various attributes of the different types of clay, it is obvious it needs some mastery.
A lot more goes into pottery than just gathering and molding a piece of clay. Depending on your needs and level of expertise, it is best to carefully distinguish the clay types, and select accordingly.
As a general rule, those who are new to the art of pottery should go for earthenware or stoneware clay. They are both very malleable, and easy to work with, and they both have similar methods of utilization, so what works for one most times, works for the other. They both can be applied in a lot of diverse pottery processes, and so, they are most suited to those who are still inexperienced.
More experienced potters can use porcelain, ball, and fire clays in addition to earthenware and stoneware clays. They can manipulate, add or substitute the clay however they see fit.